I
magine living in a home that was built in days, not months! 3D printing in real estate is bringing us closer to this reality, revolutionizing the way we build homes and structures. This technology uses a giant robotic "cake decorator" to squeeze out layers of concrete or other materials, following a computer design precisely.
The benefits of 3D printing in construction are numerous:
* Faster construction times: Homes can be built in days or weeks instead of months, saving time and money.
* Cost savings: Using less material and fewer workers on site reduces costs for builders and homebuyers.
* Design freedom: Curving walls and intricate designs that were once impossible or too expensive to build traditionally are now possible with 3D printing.
* Sustainable solutions: 3D printed buildings can be designed to be highly energy-efficient, using local materials that reduce transportation needs.
However, the cost of 3D printing a house varies widely depending on factors such as size and design complexity, location, materials, printing technology, finishes, and labor. Basic shell costs range from $45,000 to $150,000 or more, while complete homes can range from $120,000 to over $300,000.
While the lifespan of 3D printed houses is still unknown, research suggests that concrete durability could lead to a long lifespan, potentially as long as traditionally built structures. Factors impacting lifespan include materials, construction quality, climate and environment, and maintenance.
3D printed houses can be surprisingly strong due to design freedom, material properties, reinforcement, layer bonding, and disaster resistance. However, considerations such as material quality, printing process, building codes, and standards are crucial for ensuring safety and durability.
Cracking is a potential issue in 3D printed houses, caused by factors like material properties, printing process, foundation and soil issues, design flaws, and environmental factors. Mitigating the risk of cracking involves ongoing research, advancements in printing technology, stringent building codes, proper foundation and site preparation, and experienced professionals.
Real-world examples of 3D printing in real estate include Habitat for Humanity's affordable homes, Dubai's Office of the Future, and Europe's first 3D printed house. While challenges remain, such as regulation and standards, material limitations, and public perception, opportunities abound:
* Affordable housing solutions
* Disaster relief and emergency housing
* Personalized homes
As 3D printing in real estate advances, we can expect to see more widespread adoption, hybrid construction methods, smart homes and buildings, and a future where building faster, cheaper, more sustainably, and creatively becomes the norm.
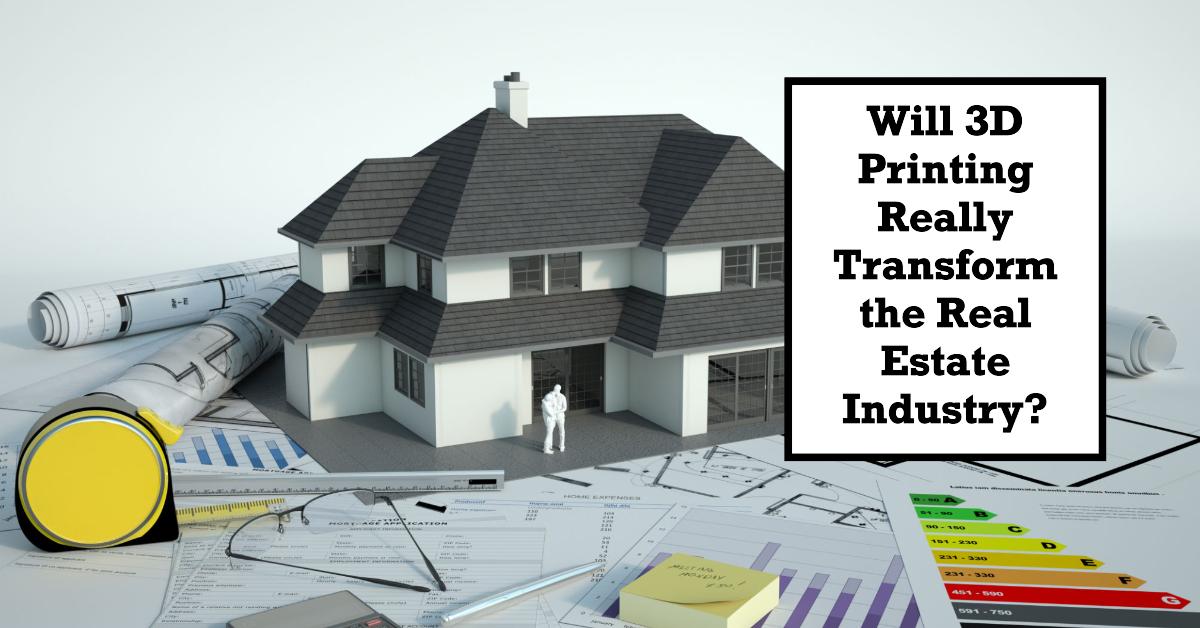