A
s the construction industry grapples with ongoing tariff uncertainty, many project stakeholders are bracing for cost escalations and supply chain disruptions. While tariffs haven't led to drastic price hikes, they have introduced a new layer of unpredictability that affects not just budgets but also schedules, procurement strategies, and design decisions.
At Timberline, we acknowledge that policy shifts and global logistics are beyond our control, but we can prepare for and respond to them effectively. Our estimating and preconstruction teams focus on developing proactive strategies, being transparent with clients, and partnering with subcontractors who share our commitment to risk management.
Recent data from Engineering News-Record (ENR) and other construction cost trackers reveals a steady climb in materials pricing across several key categories:
* Steel prices rose 11.2% by the end of 2024, with mill prices increasing another 7.1% in March 2025.
* ENR's national Materials Cost Index reported a 3% year-over-year increase by early 2025.
* Commodity metals like copper, aluminum, and steel have seen significant price increases since January, largely driven by energy costs, global demand, and trade-related friction.
These escalations may not be extreme, but they're impactful, especially when combined with existing pressures from labor shortages, aggressive schedules, and evolving building codes. To mitigate these risks, our teams employ several strategies:
1. Early procurement and pre-releasing materials: We often secure long-lead items like HVAC equipment or structural steel before contracts are signed, locking in pricing and reducing the chance of delay.
2. Transparent contracts: Our updated contract language includes tariff-related contingencies, ensuring upfront clarity on anticipated risks and making it easier for owners to understand material fluctuations.
3. Subcontractor coordination and due diligence communication: We work closely with our construction partners to identify material red flags, ensure pricing is guaranteed, and verify stable supply chains.
4. Material sourcing adjustments: We actively source "tariff-safe" materials and products from subcontractors and suppliers, creating tracking systems to evaluate costs, tariff risks, and lead times.
The degree of tariff impact varies by project type:
* New construction projects are particularly vulnerable to global price swings and lead time issues for structural steel, wood framing, and foundation materials.
* Renovations face higher risks of delays or price escalation due to mechanical, electrical, and lighting systems manufactured abroad.
* Energy code-driven upgrades in Massachusetts have added cost pressure to existing building renovations.
Tariff uncertainty persists, but we're staying ahead by locking in materials early, embedding transparency into our contracts, and maintaining close coordination with trusted subcontractors. We're happy to help clients navigate this volatility with clear plans, proactive decisions, and confidence in every step forward.
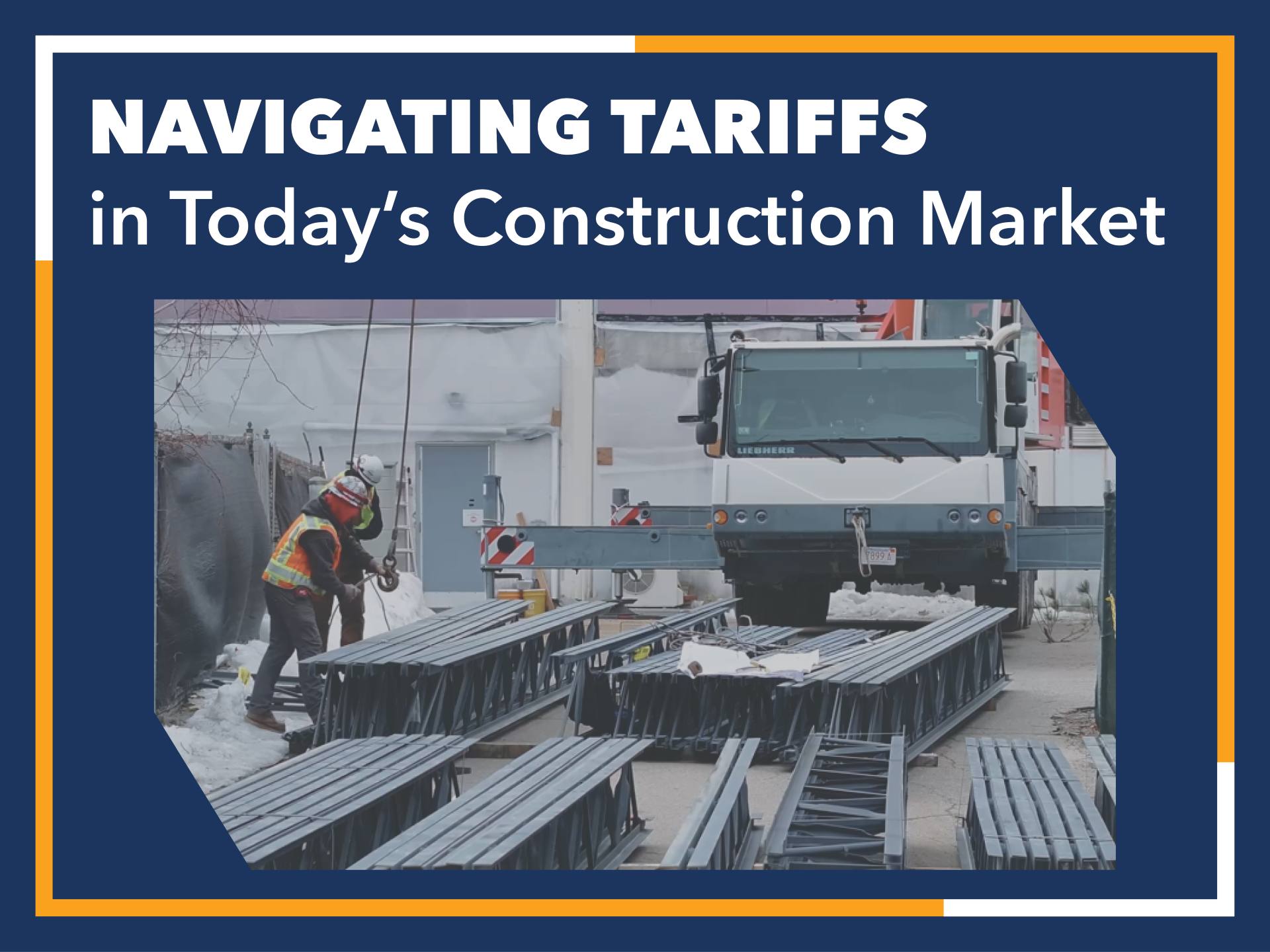